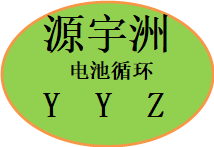
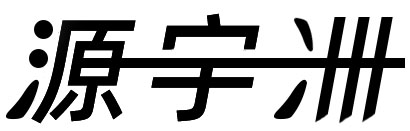

锂电池浆料和传统分散工艺
1.1,锂电池浆料的特性
锂离子电池浆料是由多种不同比重、不同粒度的原料组成,又是固-液相混合分散,形成的浆料属于非牛顿流体。锂离子电池浆料是一种像油状的流动的液体,所以具有一般流体所具有的特征如粘性、流动性等,同时因为电池浆料是一种液固两相流,所以还具有一些自身特殊的性能。
1.1.1,锂离子电池浆料流变性
流变性是指物质在外力作用下的变形和流动性质。由于液体不能承受剪切力,因而不能保持其外形的稳定。在外力的作用下,液体就会发生流动和变形等的性质,称为流变性。浆体的流变性十分复杂.一种浆体在低浓度时可能表现为牛顿流体或假塑性流体;浓度稍高产生絮团后,可能表现为宾汉流体;更高的浓度下又可能会出现胀塑性流体。
对同—种浆料,在剪切率不太高时,不出现胀流现象,剪切率高时又可能转化为胀塑性流体。有些非牛顿流体在低剪切速率和高剪切速率下都可能呈现牛顿流体形象,这可能是因为在低剪切速率下,分子的无规则热运动占优势,体现不出剪切速率对其中物料重新排列使表观粘度的变化,当剪切速率增高到一定限度后,剪切定向达到了最佳程度,因而也使表观粘度不随剪切速率而变。如前所述,许多非牛顿体其流变特性受到体系中结构变化的影响。
影响锂离子电池浆料流变性的一些主要参数:
(1)分散相或固相的类型及表面电荷的大小
对于不同种类的正负极活性物质,如正极常用的钴酸锂、锰酸锂,负极常用的石墨粉、中间相炭微球,由于其种类不同,因而具有不同的水化膨胀特性以及不同的表面电荷,这样,不同种类的活性物质其分散特性、胶溶特性以及形成具有一定强度的结构体系的能力也各不相同,其宏观表现是不同种类的活性物质配制而成的浆料具有不同的流变特性。
(2)固相的浓度
分散相或固相浓度的大小主要影响浆料的屈服应力和塑性粘度或表观粘度。在一般槽况下,固相浓度越大,其屈服应力、塑性粘度或表观粘度越大。
(3)固相颗位的大小、形状以及粒径的分布
在固相浓度不变的条件下,颗粒的粒径越小,由于其总的表面积增加,因而浆料的屈服应力和粘度将随之增加。
(4)分散介质本身的粘度。
不同的溶剂具有不同的粘度,使得浆料的粘度也将随之变化。
(5)温度和压力。
在不同的温度和压力下浆料具有不同的流变特性。
(6)浆料的PH值。
1.1.2,锂离子电池浆料触变性
触变性是指流体在剪切力作用下的一种结构破坏与恢复原有结构的效应。描述锂离子电池浆料的触变性主要包括触变的最后效果和触变过程,触变过程是指在一定的条件下锂离子电池浆料中的胶链结构随时间的破坏和恢复过程,它反映了触变性的时间效应。触变的最后效果是指在一定实验条件下达到稳定时的最大触变量。这里所说的达到稳定是指浆料内的结构破坏与恢复的一种动态平衡,而其宏观表现则为锂离子电池浆料剪切应力的固定不变,亦即剪切应力具有不随时间而变化的稳定数值。
1.1.3,分散效果对锂离子电池浆料的影响
混合分散工艺在锂离子电池的整个生产工艺中对产品的品质影响度大于30%,是整个生产工艺中最重要的环节。锂离子电池的电极制造,正极浆料由粘合剂、导电剂、正极材料等组成;负极浆料则由粘合剂、石墨碳粉等组成。正、负极浆料的制备都包括了液体与液体、液体与固体物料之间的相互混合、溶解、分散等一系列工艺过程,而且在这个过程中都伴随着温度、粘度、环境等变化。在正、负极浆料中,颗粒状活性物质的分散性和均匀性直接响到锂离子在电池两极间的运动,因此在锂离子电池生产中各极片材料的浆料的混合分散至关重要,浆料分散质量的好坏,直接影响到后续锂离子电池生产的质量及其产品的性能。
1.2,锂离子电池浆料分散机理
1.2.1,浆料稳定性理论
大部分的浆料都是属于悬浮液体系。不稳定的悬浮液在静止状态下发生絮凝,并由于重力作用而很快分层,分散的目的就是要在产品的有效期内抗絮凝、防止分层,维持悬浮颗粒的均匀分布,提高产品的稳定性。
1.2.1.1,悬浮液的絮凝理论
絮凝作用即是在静态(由于布朗运动)或动态(在剪切力作用下条件下,通过颗粒碰撞引起颗粒数目减少的过程。胶体系统中,如不考虑稳定剂,颗粒间的相互作用主要有范德华(VanderWaals)引力;伴随着带电颗粒的库仑(Coulombic)力(斥力或引力)。这些力的起因截然不同,Derjaguin和Landau在苏联,Verwey和Overbeek在荷兰分别独立的提出DLVO理论,构成了亲液分散体系中絮凝作用经典理论的基础,阐述了胶体悬浮体系的稳定性主要与胶体颗粒间上述两个独立的相互作用的相对距离有关。
1.2.1.2,悬浮液的分层理论
分层是分散相在外力(重力或离心力)作用下,在连续相中上浮或下沉的结果。在忽略布朗运动效应的静态条件下,可用Stokes定律来描述,即分散相球形颗粒由于重力的沉降速度u0由下式确定:
式中ρs-ρ为分散相与连续相的密度差,g为重力加速度,d为分散相颗粒直径,μ为连续相的粘度。如果分散相颗粒的密度比连续相密度大,颗粒下沉,速度uo为正值,反之,颗粒上浮,速度为负值。沉降速度大,浆料就容易分层。如果要保持体系稳定,就必须降低沉降速度,对于特定的浆料可以通过减小分散相固体颗粒直径d。因为只有当粒径减至连续相液体分子大小时,颗粒才能稳定、均匀地分散在液体中不发生分离。
通过以上的分析我们可以看出,要提高悬浮液的稳定性,分散相颗粒的粒径应尽量细小。但应该指出,根据前人所做的大量研究发现,随着颗粒粒度的减小,虽然颗粒由重力引起的分离作用变为次要的因素,但是由于颗粒之间的间距减小,颗粒之间的结合力(范德华力等)起到了重要决定性作用。另外,当颗粒直径小于某一细小尺寸时,此时,颗粒的布朗运动效应就不能忽略了,所以由于细小颗粒的布朗运动,而使得颗粒之间产生激烈地碰撞。若不加稳定剂,这些情况都会导致颗粒团聚,对体系的稳定是不利的。所以浆料的分散中,颗粒粒径并非越细越好,要视浆料的特性而定。分散就是要根据物料的特性与特点,减小分散相颗粒的粒度,使其分布于一个较窄的尺寸范围,并达到吸力与斥力的相互平衡,从而保证浆料体系的稳定。
1.2.2,团聚与分散的关系
浆料的团聚是指原生的微细颗粒在制备、分散及存放过程中,相互连接、由多个颗粒形成较大的颗粒团簇的现象。
颗粒在液相介质中表现为分散和团聚两种基本的行为。颗粒在液体介质中的团聚是吸附与排斥共同作用的结果,其根源是颗粒间的相互作用力。在悬浊液体系中,粉体颗粒的团聚是吸附和排斥共同作用的结果。如果吸附作用大于排斥作用,粉体颗粒团聚;如果吸附作用小于排斥作用,粉体颗粒则分散。在液体介质中,粉体颗粒受力情况较复杂,不仅有像范德华力、静电力、表面张力、毛细管力等产生团聚的吸引力,而且在粒子的表面,还会产生双电层静电作用、溶剂化膜作用、聚合物吸附层的空间保护作用等使纳米颗粒趋向于分散的斥力作用。
颗粒在介质中的稳定分散一般包括以下过程:润湿、机械分散及分散稳定。润湿通常指颗粒与颗粒之间的界面被颗粒与溶剂、分散剂等界面所取代的过程。机械分散是利用剪切力将大量颗粒细化、使团聚体解聚、被润湿、包裹吸附的过程。分散稳定是指将原生粒子或较小的团聚体在静电斥力、空间位阻斥力作用下来屏蔽范德华引力,使颗粒不再聚集的过程。团聚体分散解聚的直接原因是受到剪切力和压力的作用,剪切力在分散过程中起到了决定性的作用。
1.2.3,团聚体变形与破裂
在研究流动性质随时间和应力的变化时,一般要考察颗粒的结合与破裂。研究发现,无论是颗粒的结合所必须得碰撞,还是多颗粒团的破坏,都与颗粒大小有紧密的函数关系,也就是说,颗粒大小是影响流变和稳定性的一个关键因素。
在层流状态下,流体中的物料团聚体受层流剪切力作用。不考虑团聚体的重力作用,物料团聚体受剪切力t的作用与表面张力的作用。剪切作用的切向分力的作用效果是使团聚体发生旋转的主要原因,而法向分力和表面张力则在团聚体的内部分别产生压差,这两种压差综合作用的结果就是使团聚体的内部产生变形,在其原有裂纹的区域上就会产生应力集中,并最终导致团聚体的破碎与分散,分解成更小尺寸级别的颗粒。
在湍流状态下,流场的变化非常迅速,且存在着固体分散相与液体连续相之间的相互作用,例如由于固体相对液体相湍流具有的阻尼作用,使其脉动强度降低,流场中流动情况相当复杂。所以为了简化起见,在假定湍流是均匀的,并且是各向同性的基础上,认为液滴的破裂由湍流的脉动效应所引起的。在这种情况下,液滴受到的粘性剪切应力可忽略,若两相粘度和密度相差比较小,则在液滴表面将会产生振动,振动将会使其形状相对于平衡的球形而发生变化,当变化的程度足够大时,液滴就会不稳定,破裂成两个或更多的小液滴,条件是液滴振动的动能足以提供破裂后所增加的表面能。
1.3,浆料传统混合分散工艺
混合分散工艺在锂离子电池的整个生产工艺中对产品的品质影响度大于30%,是整个生产工艺中最重要的环节。锂离子电池的电极制造,正极浆料由粘合剂、导电剂、正极材料等组成;负极浆料则由粘合剂、石墨碳粉等组成。正、负极浆料的制备都包括了液体与液体、液体与固体物料之间的相互混合、溶解、分散等一系列工艺过程,而且在这个过程中都伴随着温度、粘度、环境等变化。在正、负极浆料中,颗粒状活性物质的分散性和均匀性直接响到锂离子在电池两极间的运动,因此在锂离子电池生产中各极片材料的浆料的混合分散至关重要,浆料分散质量的好坏,直接影响到后续锂离子电池生产的质量及其产品的性能。
目前传统的锂离子电池浆料的制备都是在双行星分散设备中完成的。尽管目前在小型电池生产技术上已日趋成熟,但目前锂离子电池的生产过程中,电池的一致性控制仍然是锂离子电池制作的技术难点,尤其是对于大容量、大功率的动力型锂离子电池。另外,随着锂离子电池材料的不断进步,原材料颗粒粒径越来越小,这不仅提高了锂离子电池性能,也非常容易形成二级团聚体,从而增加了混合分散工艺的难度。
1.3.1,正极浆料的制备(以钴酸锂为例)
正极浆料的制备过程实际上是将浆料中的各种组成按标准比例混合分散在一起,调制成浆料,以利于均匀涂布,保证极片的均匀一致性。正极制浆主要包括五个步骤,即原料的预处理、掺和、浸湿、分散和稀释。
(1)原料的物理性能
a.钴酸锂:非极性物质,不规则形状,粒径D50一般为6~8μm,含水量≤0.2%,通常为碱性,pH值为10~11。锰酸锂:非极性物质,不规则形状,粒径D50一般为5~7微米含水量≤0.2%,通常为碱性,PH值为8左右。
b.导电剂:非极性物质,葡萄链状物,吸油值约为300,粒径一般为2~5μm;主要有普通炭黑、超导炭黑、石墨乳等,在大批量应用时一般选择超导炭黑和石墨乳复配,通常为中性。
c.PVDF粘合剂:非极性物质,链状物,其分子量为300,000~1,000,000不等,吸水后分子量下降,黏性变差。
d.NMP(N-甲基吡咯烷酮):弱极性液体,用于溶解/溶胀PVDF,同时作为溶剂稀释浆料。
(2)原料的预处理
a.钴酸锂:脱水,一般用120℃常压烘烤2小时左右。
b.导电剂:脱水,一般用200℃常压烘烤2小时左右。
c.粘合剂:脱水,一般用120~140℃常压烘烤2小时左右,烘烤温度视分子量的大小决定。
d.NMP:脱水,使用干燥分子筛脱水或采用特殊取料设施,直接使用。
(3)原料的掺和
a.粘合剂的溶解(按标准浓度)及热处理。
b.钴酸锂和导电剂球磨:使粉料初步混合,钴酸锂和导电剂粘合在一起,提高团聚作用和的导电性。配成浆料后不会单独分布于粘合剂中,球磨时间一般为2小时左右;为避免混入杂质,通常使用玛瑙球作为球磨介子。
(4)粉体的分散和浸湿
固体粉末放置在空气中,随着时间的推移,将会吸附部分空气在固体的表面上,液体粘合剂加入后,液体与气体开始争夺固体表面;如果固体与气体吸附力比与液体的吸附力强,液体不能浸湿固体;如果固体与液体吸附力比与气体的吸附力强,液体可以浸湿固体,将气体挤出。当润湿角≤90度,固体浸湿。当润湿角>90度,固体不浸湿。正极材料中的所有组员都能被粘合剂溶液浸湿,所以正极粉料分散相对容易。分散方法对分散的影响:静置法(时间长,效果差,但不损伤材料的原有结构);搅拌法:自转或自转加公转(时间短,效果佳,但有可能损伤个别材料的自身结构)。
影响混合分散过程的主要参数有:
1、搅拌速度对分散速度的影响。一般说来搅拌速度越高,分散速度越快,但对材料自身结构和对设备的损伤就越大。
2、浓度对分散速度和粘结强度的影响。通常情况下浆料浓度越小,分散速度越快,但太稀将导致材料的浪费和浆料沉淀的加重。浓度越大,柔制强度越大,粘接强度越大;浓度越低,粘接强度越小。
3、真空度对分散速度的影响。高真空度有利于材料缝隙和表面的气体排出,降低液体吸附难度;材料在完全失重或重力减小的情况下分散均匀的难度将大大降低。
4、温度对分散速度的影响。适宜的温度下,浆料流动性好、易分散。太热浆料容易结皮,太冷浆料的流动性将大打折扣。
(5)稀释
加入溶剂将浆料调整为合适的浓度,便于涂布。
1.3.2,负极浆料(以石墨为例)的制备
负极浆料的制备大致与正极制浆的步骤相同。
(1)原料的物理性能
a.石墨:非极性物质,易被非极性物质污染,易在非极性物质中分散;不易吸水,也不易在水中分散。被污染的石墨,在水中分散后,容易重新团聚。一般粒径D50为20μm左右。颗粒形状多样且多不规则,主要有球形、片状、纤维状等。
b.水性粘合剂(SBR):小分子线性链状乳液,极易溶于水和极性溶剂。
c.防沉淀剂(CMC):高分子化合物,易溶于水和极性溶剂。
d.异丙醇:弱极性物质,加入后可减小粘合剂溶液的极性,提高石墨和粘合剂溶液的相容性;具有强烈的消泡作用;易催化粘合剂网状交链,提高粘结强度。乙醇:弱极性物质,加入后可减小粘合剂溶液的极性,提高石墨和粘合剂溶液的相容性;具有强烈的消泡作用;易催化粘合剂线性交链,提高粘结强度。
e.去离子水(或蒸馏水):稀释剂,酌量添加,改变浆料的流动性。
(2)原料的预处理
a.石墨:经过混合,使原料均匀化,提高一致性,然后在300~400℃常压烘烤,除去表面油性物质,提高与水性粘合剂的相容能力,修圆石墨表面棱角(有些材料为保持表面特性,不允许烘烤,否则效能降低)。
b.水性粘合剂:适当稀释,提高分散能力。
(3)掺和、浸湿和分散
a.石墨与粘合剂溶液极性不同,不易分散。
b.可先用醇水溶液将石墨初步润湿,再与粘合剂溶液混合。
c.应适当降低搅拌浓度,提高分散性。
d.分散过程为减少极性物与非极性物距离,提高势能或表面能,所以为吸热反应,搅拌时总体温度有所下降。如条件允许应该适当升高搅拌温度,使吸热变得容易,同时提高流动性,降低分散难度。
e.搅拌过程如加入真空脱气过程,排除气体,促进固-液吸附,效果更佳。
(4)稀释
加入溶剂将浆料调整为合适的浓度,便于涂布。
2.3.3,传统分散工艺面临的问题
(1)根据传统工艺中的叶轮剪切/循环特性,可以把叶轮的作用分为两大类,第一类是对叶轮附近产生的剪切作用;第二类则是通过叶轮泵出的流量产生循环作用。浆体的进一步分散作用主要依靠叶轮的剪切作用,而叶轮的流量决定了叶轮的分散的能力。而在离叶轮端部较远的区域,总会存在一层浆料始终停滞不动,这个区域也就是人们常说的“死区”,分散设备的工作区域越大,而且浆料黏度越高,“死区”的问题就越突出,就算采用不同的叶轮和结构,死区仍然难以避免,因此在锂离子电池浆料的制备过程中,所制得的浆料产品就会出现混合分散不均匀、粉体颗粒与粘合剂接触不均匀、易分层和发生硬性沉淀等一系列问题。
(2)在操作过程中双行星搅拌也会遇到诸多问题:
1.批次分散工艺,混合分散时间长,能量消耗大。
2.电极粉末材料由行星搅拌器顶部加入,粉尘容易飞扬、漂浮。更重要的是粉末与液相混合极易发生团聚。
3.物料易残留于行星搅拌器的罐盖、罐壁及搅拌桨上,清洗操作困难。
4.空气易存留于分散混合罐,气泡的产生影响分散效果。
5.批次工艺致使量产受到限制,生产线占地面的大,维护成本高。